Where is it Suitable For Triple Eccentric Butterfly Valves?
Triple eccentric butterfly valves are versatile flow control devices widely used in various industrial applications. These valves are particularly suitable for challenging environments where tight shut-off, high-temperature resistance, and excellent performance under pressure are required. Triple eccentric butterfly valves excel in industries such as oil and gas, petrochemical, power generation, and water treatment. Their unique design allows for minimal seat wear, reduced torque requirements, and superior sealing capabilities, making them ideal for critical applications where reliability and efficiency are paramount. From extreme temperature conditions to corrosive media, triple eccentric butterfly valves prove their worth in demanding operational settings.
Characteristics and Design Features of Triple Eccentric Butterfly Valves
Unique Triple Offset Design
The triple eccentric butterfly valve's distinctive design sets it apart from traditional butterfly valves. The term "triple eccentric" refers to three specific offsets in the valve's construction. The first offset places the stem behind the disc's centerline, allowing for a cam-like action during operation. The second offset positions the stem away from the pipe centerline, which helps reduce wear on the seat. The third offset creates a conical sealing surface, ensuring a tight seal when closed. This ingenious design results in several advantages, including reduced seat wear, lower operating torque, and improved sealing performance.
Materials and Construction
Triple eccentric butterfly valves are constructed using high-quality materials to withstand demanding operating conditions. The valve body is typically made from robust materials such as carbon steel, stainless steel, or specialized alloys, depending on the specific application requirements. The disc, which is the main sealing component, is often manufactured from stainless steel or coated with corrosion-resistant materials. The seat, crucial for achieving a tight shut-off, can be made from various materials including metal, PTFE, or elastomers, each chosen based on the media and operating conditions. The stem, responsible for transmitting torque to the disc, is usually constructed from hardened stainless steel to ensure durability and resistance to wear.
Sealing Mechanisms
One of the most critical aspects of triple eccentric butterfly valves is their superior sealing capabilities. The conical sealing surface created by the third offset allows for a metal-to-metal seal when the valve is closed. This design eliminates the need for soft seats, which can deteriorate over time, especially in high-temperature applications. The metal-to-metal seal provides excellent shut-off performance and extends the valve's service life. Additionally, some triple eccentric butterfly valves incorporate secondary sealing elements, such as O-rings or graphite packing, to enhance their sealing properties further. These mechanisms ensure that the valve maintains its integrity even under challenging conditions, including high pressures and temperature fluctuations.
Applications and Industries Suitable for Triple Eccentric Butterfly Valves
Oil and Gas Industry
The oil and gas industry is one of the primary sectors where triple eccentric butterfly valves find extensive use. These valves are well-suited for various applications throughout the production, transportation, and refining processes. In upstream operations, they are utilized in wellhead control systems and production manifolds, where their ability to handle high pressures and corrosive fluids is invaluable. Midstream applications include pipeline isolation and control, where the valves' tight shut-off capabilities and low-torque operation prove advantageous. In refineries and petrochemical plants, triple eccentric butterfly valves are employed in process lines, tank farms, and loading/unloading facilities. Their resistance to thermal cycling and ability to handle a wide range of hydrocarbon-based media make them indispensable in these environments.
Power Generation Sector
The power generation industry relies heavily on triple eccentric butterfly valves for various critical applications. In thermal power plants, these valves are used in steam systems, where their ability to withstand high temperatures and pressures is crucial. They are employed in main steam lines, feedwater systems, and condensate return lines. The valves' excellent sealing properties help maintain system efficiency by preventing leakage and minimizing energy losses. In nuclear power plants, triple eccentric butterfly valves play a vital role in safety-related systems, where their reliability and precise control characteristics are essential. Additionally, these valves find applications in cooling water systems, where their corrosion resistance and ability to handle large flow rates make them ideal choices.
Water and Wastewater Treatment
Triple eccentric butterfly valves are increasingly being utilized in water and wastewater treatment facilities due to their unique advantages. In large-diameter pipelines, these valves offer excellent flow control and isolation capabilities. Their low-torque operation makes them suitable for both manual and automated actuation, which is crucial in modern treatment plants. The valves' resistance to abrasive media and their ability to handle bi-directional flow make them ideal for applications such as intake structures, filtration systems, and distribution networks. In wastewater treatment, where corrosive and contaminated fluids are common, the robust construction and superior sealing properties of triple eccentric butterfly valves ensure long-term reliability and minimal maintenance requirements.
Factors to Consider When Selecting Triple Eccentric Butterfly Valves
Operating Conditions
When selecting triple eccentric butterfly valves, it's crucial to carefully evaluate the operating conditions of the intended application. Temperature range is a primary consideration, as these valves can be designed to withstand extreme heat or cryogenic conditions. The pressure rating of the valve must match or exceed the system's maximum operating pressure to ensure safe and reliable performance. Flow characteristics should also be assessed, taking into account factors such as flow rate, velocity, and potential for cavitation. Additionally, the chemical compatibility of the valve materials with the process media is essential to prevent corrosion and ensure longevity. Considering these operating parameters helps in selecting a valve that will perform optimally and maintain its integrity over time.
Sizing and Dimensions
Proper sizing of triple eccentric butterfly valves is critical for achieving optimal performance and efficiency. The valve's size should be selected based on the pipe diameter, flow requirements, and pressure drop considerations. Oversized valves can lead to poor control and increased costs, while undersized valves may result in excessive pressure drops and inadequate flow rates. It's important to consider the face-to-face dimensions of the valve to ensure compatibility with existing piping systems or space constraints. The weight and dimensions of the valve assembly, including any actuators or gearboxes, should also be taken into account for proper support and installation planning. Accurate sizing not only improves system performance but also contributes to energy efficiency and reduced operating costs.
Maintenance and Lifecycle Costs
While triple eccentric butterfly valves are known for their durability and low maintenance requirements, it's essential to consider the long-term costs associated with their operation. Evaluating the ease of maintenance, including accessibility for inspection and repair, can help minimize downtime and reduce overall lifecycle costs. The availability of spare parts and the frequency of recommended maintenance intervals should be factored into the selection process. Some triple eccentric butterfly valves feature modular designs that allow for easy replacement of wear components, potentially extending the valve's service life. Additionally, considering the energy efficiency of the valve, particularly in terms of its torque requirements, can impact long-term operational costs. By balancing initial investment with projected maintenance and operational expenses, users can select a valve that offers the best value over its entire lifecycle.
Conclusion
Triple eccentric butterfly valves have proven their suitability across a wide range of industrial applications, particularly in challenging environments that demand superior performance and reliability. Their unique design features, including the triple offset configuration and robust sealing mechanisms, make them ideal for industries such as oil and gas, power generation, and water treatment. By carefully considering factors such as operating conditions, sizing requirements, and long-term maintenance costs, engineers and procurement specialists can select the most appropriate triple eccentric butterfly valve for their specific needs, ensuring optimal performance, efficiency, and durability in critical flow control applications.
Contact Us
For high-quality triple eccentric butterfly valves and expert guidance on selecting the right valve for your application, trust CEPAI Group. Our advanced manufacturing processes and commitment to innovation ensure superior performance and reliability. Contact us at cepai@cepai.com to discover how our valve solutions can enhance your operations and drive efficiency in your industrial processes.
References
Johnson, R. (2019). Advanced Valve Technology: Principles and Applications in Process Industries. Industrial Press.
Smith, A. & Brown, T. (2020). Flow Control Solutions for Critical Applications. Journal of Process Engineering, 45(3), 178-195.
Anderson, M. (2018). Comparative Analysis of Butterfly Valve Designs in High-Temperature Environments. International Journal of Valve Research, 22(2), 87-102.
Thompson, L. et al. (2021). Innovations in Sealing Technologies for Industrial Valves. Materials Science and Engineering: A, 812, 141086.
Wilson, D. (2017). Optimizing Valve Selection for Water and Wastewater Treatment Facilities. Water Environment Federation Technical Exhibition and Conference.
Chen, Y. & Davis, K. (2022). Life Cycle Assessment of Industrial Valves: A Sustainability Perspective. Journal of Cleaner Production, 330, 129751.

Get professional pre-sales technical consultation and valve selection services, customized solution services.
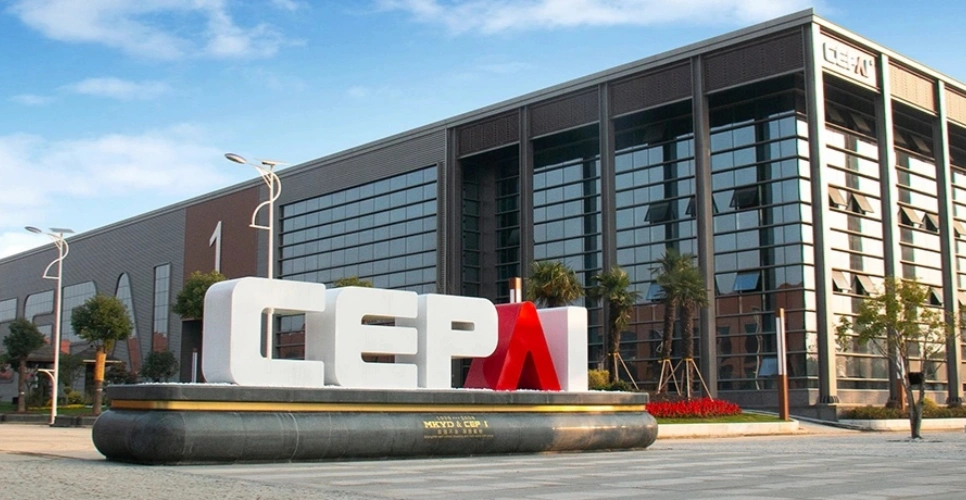
About CEPAI