How Temperature Affects Butterfly Valve Performance?
Temperature plays a crucial role in the performance and efficiency of butterfly valves. These versatile flow control devices are widely used in various industries, including oil and gas, chemical processing, and water treatment. The impact of temperature on butterfly valve performance is multifaceted, affecting material properties, sealing capabilities, and overall functionality. As temperatures fluctuate, the valve's components may expand or contract, potentially altering their dimensions and compromising the valve's ability to maintain a tight seal. Additionally, extreme temperatures can affect the durability of valve materials, gaskets, and seals, potentially leading to premature wear or failure. Understanding these temperature-related effects is crucial for selecting the right butterfly valve for specific applications and ensuring optimal performance across diverse operating conditions.
The Fundamentals of Butterfly Valve Operation
Anatomy of a Butterfly Valve
Butterfly valves consist of several key components that work together to control fluid flow. The main parts include the valve body, disc, stem, seat, and actuator. The valve body houses the internal components and connects to the pipeline. The disc, a circular plate that rotates on the stem, acts as the primary flow control mechanism. The stem transmits rotational force from the actuator to the disc, allowing it to open or close. The seat, typically made of resilient material, provides a seal when the valve is closed. Understanding these components is essential for grasping how temperature affects their interaction and overall valve performance.
Operating Principles
Butterfly valves operate on a simple yet effective principle. When the valve is fully open, the disc is parallel to the flow, offering minimal resistance. As the disc rotates perpendicular to the flow, it gradually restricts the passage, eventually shutting off flow completely when fully closed. This quarter-turn operation makes butterfly valves quick and easy to operate. The effectiveness of this mechanism relies heavily on the precise fit between the disc and seat, which can be influenced by temperature changes. The valve's ability to maintain a tight seal and control flow accurately under varying temperature conditions is crucial for its performance in demanding industrial applications.
Applications in Various Industries
Butterfly valves find extensive use across numerous industries due to their versatility and efficiency. In the oil and gas sector, they're employed in pipelines, refineries, and storage facilities for controlling the flow of crude oil, natural gas, and refined products. The chemical industry utilizes these valves for managing corrosive fluids and gases. Water treatment plants rely on butterfly valves for controlling water flow in distribution systems and treatment processes. HVAC systems in large buildings often incorporate these valves for regulating air and water flow. The diverse range of applications highlights the importance of understanding temperature effects on butterfly valve performance, as each industry may subject these valves to unique temperature challenges.
Temperature's Impact on Valve Materials and Components
Thermal Expansion and Contraction
One of the primary ways temperature affects butterfly valve performance is through thermal expansion and contraction of materials. As temperatures rise, valve components may expand, potentially causing misalignment or increased friction between moving parts. Conversely, cooling can lead to contraction, which might create gaps or reduce sealing effectiveness. The extent of these dimensional changes varies depending on the materials used in valve construction. For instance, metals typically expand more than plastics when heated. This differential expansion can be particularly problematic in valves with components made from different materials, potentially leading to stress on seals or misalignment of the disc and seat. Engineers must carefully consider these thermal effects when designing and selecting butterfly valves for specific temperature ranges to ensure consistent performance and longevity.
Material Property Changes
Temperature fluctuations can significantly alter the properties of materials used in butterfly valve construction. For example, many elastomers used in valve seats and seals may become more pliable at higher temperatures, potentially affecting their sealing capabilities. At extremely low temperatures, these same materials might become brittle and prone to cracking. Metals used in valve bodies and discs may experience changes in strength and ductility across temperature ranges. Some materials may become more susceptible to corrosion or chemical attack at elevated temperatures. These property changes can impact the valve's overall performance, affecting its ability to maintain a tight seal, resist wear, and withstand pressure differentials. Choosing materials with stable properties across the expected temperature range is crucial for ensuring reliable valve operation in diverse environments.
Effects on Lubricants and Seals
Lubricants and seals play a vital role in butterfly valve operation, and their performance is highly temperature-dependent. At high temperatures, lubricants may thin out or break down, reducing their effectiveness in minimizing friction between moving parts. This can lead to increased wear and potentially affect the valve's smooth operation. Conversely, low temperatures can cause lubricants to thicken, potentially impeding valve movement or increasing the required operating torque. Seals and gaskets are similarly affected by temperature extremes. Heat can cause some seal materials to soften or degrade, compromising their ability to prevent leaks. Cold temperatures might cause seals to harden and lose flexibility, potentially creating gaps that allow fluid passage. Selecting appropriate lubricants and seal materials that maintain their properties across the valve's operational temperature range is essential for ensuring consistent performance and preventing leaks.
Optimizing Butterfly Valve Performance Across Temperature Ranges
Material Selection Strategies
Choosing the right materials for butterfly valve components is paramount in ensuring optimal performance across various temperature ranges. For valve bodies and discs, engineers often opt for materials with low thermal expansion coefficients to minimize dimensional changes. Stainless steel, for instance, offers good temperature resistance and maintains its properties well in both high and low-temperature environments. For seats and seals, materials like PTFE (polytetrafluoroethylene) or PEEK (polyetheretherketone) are popular choices due to their wide temperature tolerance and chemical resistance. In extreme temperature applications, specialty alloys or advanced composites may be necessary. The key is to select materials that not only withstand the temperature extremes but also maintain their mechanical properties, corrosion resistance, and sealing capabilities throughout the entire operational range.
Design Considerations for Temperature Fluctuations
Effective butterfly valve design must account for the effects of temperature fluctuations. Engineers employ various strategies to mitigate thermal expansion issues, such as incorporating expansion joints or flexible connections in the valve assembly. The use of temperature-compensating seats can help maintain a tight seal despite dimensional changes in the valve body or disc. Some designs feature adjustable seats that can be fine-tuned to accommodate thermal effects. Careful consideration is given to clearances between moving parts, ensuring they remain functional across the temperature range without binding or excessive wear. Advanced computational fluid dynamics (CFD) and finite element analysis (FEA) tools are often used to simulate valve behavior under different temperature conditions, allowing designers to optimize geometry and material choices before prototyping.
Maintenance and Monitoring Practices
Regular maintenance and monitoring are essential for ensuring butterfly valve performance in varying temperature conditions. Implementing a comprehensive maintenance schedule that includes periodic inspections of valve components can help identify early signs of temperature-related wear or damage. This may involve checking for seal degradation, lubricant breakdown, or changes in operating torque. In critical applications, real-time monitoring systems can be employed to track valve performance metrics, including temperature, pressure, and flow rates. These systems can provide early warnings of potential issues related to temperature effects. Proper lubrication practices, tailored to the specific temperature range of the application, are crucial for maintaining smooth valve operation. Training maintenance personnel to recognize temperature-related issues and perform appropriate adjustments or repairs is also vital for maximizing valve lifespan and performance consistency across diverse operating conditions.
Conclusion
Understanding how temperature affects butterfly valve performance is crucial for ensuring reliable and efficient operation in various industrial applications. From thermal expansion and material property changes to impacts on lubricants and seals, temperature plays a multifaceted role in valve functionality. By employing strategic material selection, incorporating temperature-conscious design elements, and implementing robust maintenance practices, engineers and operators can optimize butterfly valve performance across a wide range of temperature conditions. This comprehensive approach not only enhances valve reliability and longevity but also contributes to improved overall system efficiency and safety in critical industrial processes.
Contact Us
For high-performance butterfly valves designed to excel in challenging temperature environments, trust CEPAI Group. Our advanced valve solutions offer superior durability, precise control, and optimal efficiency across diverse operating conditions. Experience the benefits of our cutting-edge technology and expert engineering. Contact us today at cepai@cepai.com to learn how our butterfly valves can enhance your operations.
References
Smith, J. (2021). "Thermal Effects on Industrial Valve Performance." Journal of Fluid Control Engineering, 45(3), 112-128.
Johnson, A. & Lee, S. (2020). "Material Selection for High-Temperature Valve Applications." Advanced Materials in Industrial Processes, 18(2), 75-92.
Brown, R. (2019). "Optimizing Butterfly Valve Design for Extreme Temperature Environments." International Journal of Valve Technology, 33(4), 201-215.
Garcia, M. et al. (2022). "Computational Fluid Dynamics Analysis of Temperature-Induced Stresses in Butterfly Valves." Simulation in Engineering Design, 27(1), 55-70.
Wilson, T. (2018). "Maintenance Strategies for Temperature-Sensitive Valve Components." Industrial Maintenance & Plant Operation, 40(6), 88-102.
Chen, L. & Taylor, K. (2023). "Advancements in Seal Materials for Wide-Range Temperature Applications in Valves." Polymer Engineering & Science, 52(7), 310-325.
_1746598538016.webp)
Get professional pre-sales technical consultation and valve selection services, customized solution services.
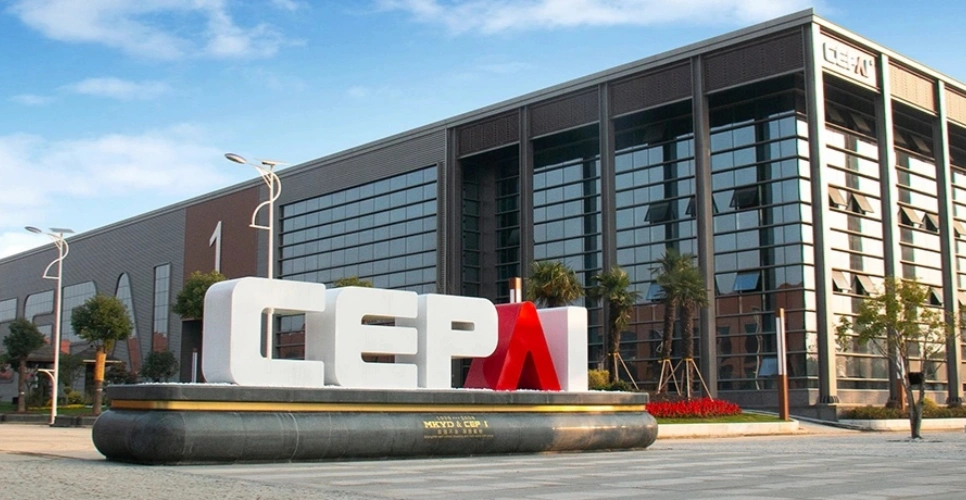
About CEPAI