Top Tips for Calibrating and Maintaining Pressure Transmitters
When it comes to keeping your oil and gas operations running smoothly, the accuracy of your pressure transmitter is non-negotiable. These devices are the backbone of monitoring and controlling critical processes, ensuring safety, efficiency, and reliability. But how do you keep them performing at their best? Regular calibration and maintenance are the keys to unlocking their full potential. By following a few expert tips, you can extend the lifespan of your equipment, reduce downtime, and avoid costly errors. Whether you're handling wellhead devices or pipeline valves, these practical steps will help you maintain precision and performance in even the most demanding environments.
Understanding the Basics of Pressure Transmitters
What Makes Pressure Transmitters Essential in Oil and Gas?
Pressure transmitters play a pivotal role in the oil and gas industry, especially in high-stakes environments like drilling and production. These sophisticated instruments measure the pressure of gases or liquids and convert the data into an electrical signal, which is then used to monitor and control processes. From ensuring the safe operation of wellhead devices to maintaining the integrity of pipeline valves, their accuracy is crucial. A malfunctioning or poorly calibrated pressure transmitter can lead to inaccurate readings, compromising safety and efficiency. By understanding their importance, you can better appreciate the need for meticulous care and regular upkeep.
Common Challenges in Pressure Transmitter Performance
Even the most advanced pressure transmitters face challenges that can affect their performance. Exposure to harsh conditions, such as extreme temperatures, corrosive substances, or high vibration, can degrade their accuracy over time. Additionally, issues like drift - where the device's output gradually shifts away from the true value - can occur if calibration is neglected. Blockages in sensing lines, electrical interference, and improper installation are other hurdles that can compromise functionality. Recognizing these challenges is the first step toward addressing them effectively, ensuring your equipment delivers reliable data and supports seamless operations.
Key Components That Require Attention
To maintain optimal performance, it's essential to focus on the critical components of a pressure transmitter. The sensor, which detects pressure changes, is the heart of the device and must be free from damage or contamination. The diaphragm, often exposed to process fluids, needs regular inspection for signs of wear or corrosion. The electronics, responsible for signal conversion, should be checked for stability and protected from environmental factors like moisture or extreme heat. By paying close attention to these elements, you can prevent minor issues from escalating into major failures, keeping your operations running smoothly.
Best Practices for Calibrating Pressure Transmitters
Setting Up a Calibration Schedule
Calibration is the cornerstone of ensuring your pressure transmitter delivers accurate measurements. Establishing a regular calibration schedule is vital, but the frequency depends on factors like the device's application, environmental conditions, and manufacturer recommendations. For instance, transmitters used in critical applications, such as emergency cut-off valves, may require monthly checks, while those in less demanding roles might need calibration every six months. Use historical data and performance trends to fine-tune your schedule, ensuring you strike a balance between over-maintenance and neglect. A well-planned schedule minimizes downtime and maximizes reliability, keeping your operations on track.
Choosing the Right Calibration Tools
The accuracy of your calibration process hinges on the quality of the tools you use. Invest in high-precision equipment, such as deadweight testers or digital calibrators, to ensure your pressure transmitter is aligned with industry standards. These tools should be regularly certified to guarantee their accuracy, especially if you're working in a regulated environment like oil and gas. Additionally, consider using software solutions that can automate data logging and analysis, reducing the risk of human error. By selecting the right tools, you can achieve consistent, repeatable results, bolstering the credibility of your measurements.
Step-by-Step Calibration Process
Calibrating a pressure transmitter requires a methodical approach to ensure precision. Begin by isolating the device from the process to avoid interference, then connect it to your calibration equipment. Apply a series of known pressures across the transmitter's range, comparing the output to the expected values. Adjust the zero and span settings as needed to correct any discrepancies. Document each step meticulously, noting the as-found and as-left conditions to track performance trends over time. Once calibration is complete, perform a final verification to confirm accuracy before returning the device to service. This systematic process ensures your equipment remains dependable and compliant.
Proactive Maintenance Strategies for Longevity
Routine Inspections and Cleaning
Preventive maintenance is the key to extending the lifespan of your pressure transmitter. Conduct routine inspections to identify signs of wear, corrosion, or damage, particularly in components exposed to harsh process fluids. Clean the sensing lines and diaphragm regularly to prevent blockages or buildup that could skew readings. Use appropriate cleaning agents that won't harm the device's materials, and always follow manufacturer guidelines. By staying proactive, you can catch potential issues early, avoiding unplanned downtime and costly repairs. Regular upkeep also ensures your equipment meets the stringent standards of the oil and gas industry.
Environmental Protection Measures
The harsh environments typical of oil and gas operations can take a toll on pressure transmitters, making environmental protection a priority. Install protective enclosures or heat shields to guard against extreme temperatures, and use vibration dampeners to mitigate the effects of mechanical stress. In corrosive environments, consider transmitters with specialized coatings or materials, such as those designed for offshore applications. Additionally, ensure proper sealing to prevent moisture ingress, which can damage electronics. By shielding your equipment from external stressors, you can enhance its durability and maintain consistent performance, even in the toughest conditions.
Troubleshooting Common Issues
Even with diligent maintenance, pressure transmitters can encounter issues that require troubleshooting. If you notice erratic readings, check for electrical interference or grounding problems, which can often be resolved by rerouting cables or improving grounding connections. For drift or zero-shift issues, recalibration may be necessary, but also inspect the sensor for signs of damage or contamination. Blockages in sensing lines can cause delayed or inaccurate responses, so flush the lines and verify their integrity. Keeping a detailed log of symptoms and solutions can help you identify patterns and address recurring problems more efficiently, ensuring your equipment remains operational.
Conclusion
Calibrating and maintaining pressure transmitters doesn't have to be daunting. By understanding their role, adopting best practices for calibration, and implementing proactive maintenance, you can ensure these vital devices perform reliably in your oil and gas operations. Regular care not only enhances accuracy but also extends equipment lifespan, saving you time and resources. Stay vigilant, use the right tools, and protect your devices from environmental challenges to keep your processes running smoothly.
Contact Us
Looking for top-quality pressure transmitters and expert support? CEPAI Group offers cutting-edge solutions for oil and gas applications, backed by global certifications and innovative technology. Contact us today at cepai@cepai.com to elevate your operations with reliable, high-performance equipment.
References
"Instrumentation for Oil and Gas: A Practical Guide to Pressure Measurement" - Published by Elsevier, 2019.
"Calibration Techniques for Industrial Pressure Sensors" - Journal of Process Control, Volume 28, 2020.
"Maintenance Strategies for Instrumentation in Harsh Environments" - Oil & Gas Engineering Review, 2021.
"Fundamentals of Pressure Transmitter Technology" - Automation World Magazine, Issue 14, 2018.
"Environmental Impacts on Process Instrumentation" - Chemical Engineering Progress, Volume 116, 2022.
"Best Practices in Calibration for Oilfield Equipment" - International Society of Automation, Technical Paper, 2020.

Get professional pre-sales technical consultation and valve selection services, customized solution services.
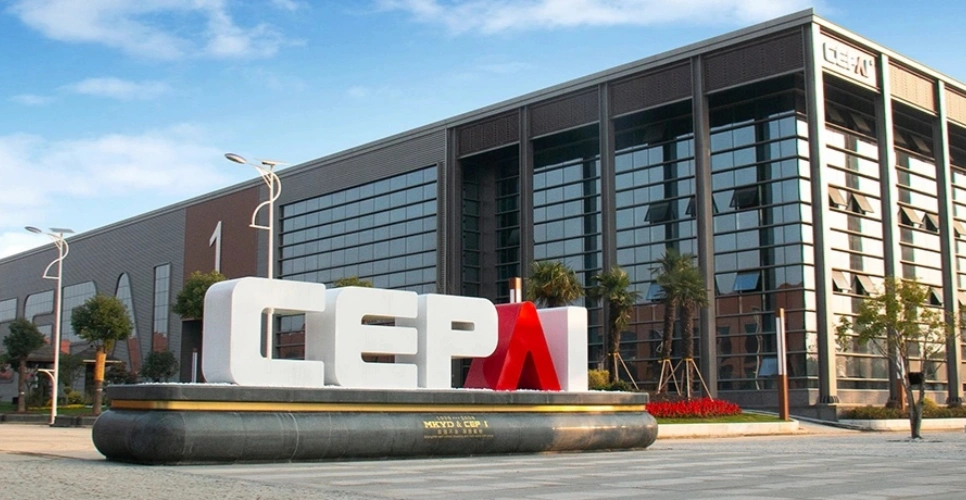
About CEPAI